Finding Electronics Manufacturing Services (EMS)
Electronics contract manufacturers, also called ECMs, offer a range of services. From PCB assembly to full product assembly, they help businesses scale production.
But how do you find the right one? What factors should you consider?
This guide aims to answer these questions. It provides actionable steps to help you find a reliable electronics contract manufacturer. Whether you’re a business owner, procurement manager, or engineer, this guide is designed to help you make an informed decision for your manufacturing needs.
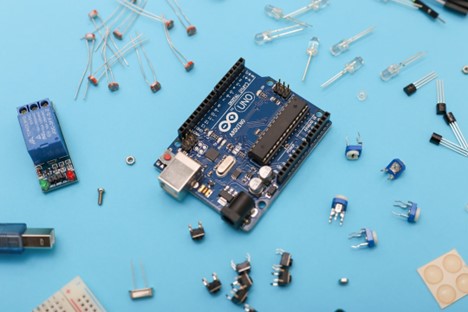
Understanding Electronics Contract Manufacturing
Electronics contract manufacturing is a form of outsourcing. Companies hire contract manufacturers to produce electronic components or assemblies.
By outsourcing to an electronics contract manufacturer, companies can scale production without making significant capital investments in equipment or facilities. This allows companies to focus on their core competencies. They can leave the manufacturing process to experts.
What is EMS in Manufacturing?
Electronic Manufacturing Services (EMS), sometimes referred to as Electronic Contract Manufacturing (ECM), is the term for a broad range of functions, from design and production to assembly and testing for electronics manufacturing.
Here’s a brief list of services they typically offer:
- PCB assembly (PCBA)
- Prototyping
- Full product assembly
- Wire harness manufacturing
- Testing and quality assurance
Hankscraft is a full-service contract manufacturing company, with expertise in electronic and electromechanical manufacturing and assembly. We have proven capabilities in a wide range of electronic manufacturing types, including PCBA fulfillment, wire harness manufacturing, cable assemblies, and sourcing within a trusted global vendor network.
In the next sections, we’ll delve deeper into the role of electronics contract manufacturers. We’ll also discuss how to select the right one for your needs.
The Role of Electronics Contract Manufacturers
Electronics contract manufacturers play a crucial role in the supply chain. They provide the expertise and resources needed to produce electronic components and assemblies.
These contract manufacturing companies can help businesses scale their production. They can do this without the need for significant capital investment. This is particularly beneficial for small and medium-sized businesses.
Businesses seeking manufacturing can benefit significantly from scaling their production with a contract manufacturer, due to high-volume capabilities and competitive pricing.
In addition to manufacturing, some contract manufacturing companies, like Hankscraft, offer a full range of services, including design assistance, logistics, sourcing, etc. They can help optimize product designs for manufacturability. This can lead to cost savings and improved product quality.
In essence, electronics contract manufacturers are partners. They work closely with their clients to ensure the successful production of electronic products. They play a vital role in bringing products from concept to market.
Criteria for Selecting the Right Electronics Contract Manufacturer
Choosing the right electronics contract manufacturer is a critical decision. It can significantly impact the success of your product. There are several factors to consider when making this choice.
Experience is a key factor. A manufacturer with a proven track record in your industry is a valuable asset. They will understand the unique challenges and requirements of your sector.
Certifications are another important consideration. These demonstrate a manufacturer’s commitment to quality and compliance. Look for certifications like ISO 9001, ISO 13485 for medical devices, or AS9100 for aerospace.
Technological capabilities should also be evaluated. The manufacturer should have the necessary equipment and expertise to produce your product. They should also be able to adapt to new technologies and processes.
Consider the following criteria when selecting an electronics contract manufacturer:
- Experience in your industry
- Relevant certifications
- Technological capabilities
- Financial stability
- Quality control processes
- Communication and customer service
- Geographic location
- Flexibility and scalability
- Intellectual property protection
- Custom solutions and design assistance
Remember, the goal is to find a partner. You want a manufacturer who will work with you to achieve your objectives. Take the time to thoroughly evaluate potential manufacturers. This will ensure you make the best choice for your business.
Certifications and Compliance: Ensuring Quality and Safety
Certifications are a key indicator of a manufacturer’s commitment to quality. They show that the manufacturer adheres to industry standards. This is crucial in industries like medical devices or aerospace.
Certifications for Electronics Contract Manufacturing
Certifications from the Insitute for Printed Circuits (IPC), such as IPC-A-610, are a key indicator of quality assurance for EMS. The IPC sets standards and provides certifications for companies to authorize quality electronics production.
Electronics Contract Manufacturers who have staff who oversee quality and reliability of their EMS could consider earning a certification such as IPC-A-610. Topics covered in the training include guidelines for various PCB components, such as Surface Mount Technology (SMT), socket pins, card edge connectors, and much more.
Other important certifications include ISO 9001, a certification indicating a robust quality management system. It shows that the manufacturer is committed to continuous improvement. This can give you confidence in their ability to deliver high-quality products.
ISO 13485 certification is specific to medical devices. It demonstrates compliance with stringent quality and safety requirements. If you’re in the medical field, this certification is a must-have.
AS9100 certification is for the aerospace industry. It covers a wide range of manufacturing processes. This certification ensures that the manufacturer can meet the complex and rigorous demands of aerospace manufacturing.
In conclusion, certifications are a vital consideration when choosing an electronics contract manufacturer. They provide assurance of quality, safety, and compliance.
Hankscraft is committed to quality, safety and helping customers navigate regulatory compliance in manufacturing. We have experience manufacturing products that meet UL and CSA standards. Our global manufacturing facility is ISO 9001:2015 certified.
Evaluating Technological Capabilities and Services Offered
The technological capabilities of a manufacturer are a key factor. They determine the complexity and quality of the products they can produce. A manufacturer with advanced capabilities can offer more sophisticated solutions.
It’s also important to consider the range of services offered. Some manufacturers offer a full suite of services. These can include design, prototyping, assembly, and testing. Others may specialize in certain areas.
The manufacturer’s ability to adapt to new technologies is also crucial. This can impact their efficiency and the quality of their output. It can also affect their ability to meet your future needs.
Consider also the manufacturer’s experience with your specific product type. This can influence their understanding of your needs and their ability to meet them.
In summary, a manufacturer’s technological capabilities and services offered are key considerations. They can impact the quality, cost, and timeline of your project.
Hankscraft’s Electronic Manufacturing Services
Hankscraft offers experienced staff and proven success in providing EMS. For over 100 years, Hankscraft has been serving trusted contract manufacturing services to our customers, including complex and detailed electronic parts and projects.
As a customer of Hankscraft, you’ll reap the benefits of a full-service contract manufacturing company with trusted resources for PCBs, wire harnesses and cable assemblies. Contact us today to put your electronic manufacturing project in capable hands.
PCB Manufacturing Capabilities
Printed Circuit Board (PCB) manufacturing capabilities encompass a wide range of processes and technologies essential for producing electronic components. Some common types of PCB manufacturing capabilities include:
- Surface Mount Technology (SMT): SMT is a widely used method for assembling electronic circuits. Components are mounted directly onto the surface of the PCB, allowing for smaller and more densely packed boards.
- Through-Hole Technology (THT): THT involves mounting components with wire leads through holes in the PCB. This method is known for its reliability and strength, making it suitable for components requiring mechanical stability.
- Multilayer PCBs: Multilayer PCBs consist of multiple layers of copper traces separated by insulating material. They provide increased design flexibility and are commonly used in complex electronic devices.
- Flexible PCBs: Flexible PCBs are designed to be bent, twisted, or folded to fit into tight spaces or unique form factors. They are ideal for applications where traditional rigid PCBs are not suitable.
- Rigid-Flex PCBs: Rigid-flex PCBs combine the benefits of both rigid and flexible PCBs. They consist of rigid sections connected by flexible circuits, offering improved reliability and space savings.
- High-Frequency PCBs: High-frequency PCBs are designed to handle signals in the GHz range. They are used in applications such as telecommunications, radar systems, and high-speed data transfer.
- High-Density Interconnect (HDI) PCBs: HDI PCBs feature high-density wiring and compact designs. They allow for more connections in a smaller area, making them ideal for miniaturized electronic devices.
- Metal Core PCBs: Metal core PCBs have a metal core that acts as a heat sink, dissipating heat more efficiently. They are commonly used in applications requiring high thermal conductivity.
These are just a few examples of the diverse PCB manufacturing capabilities available to meet the varying needs of electronic products. Understanding these capabilities can help you choose the right manufacturer for your specific requirements.
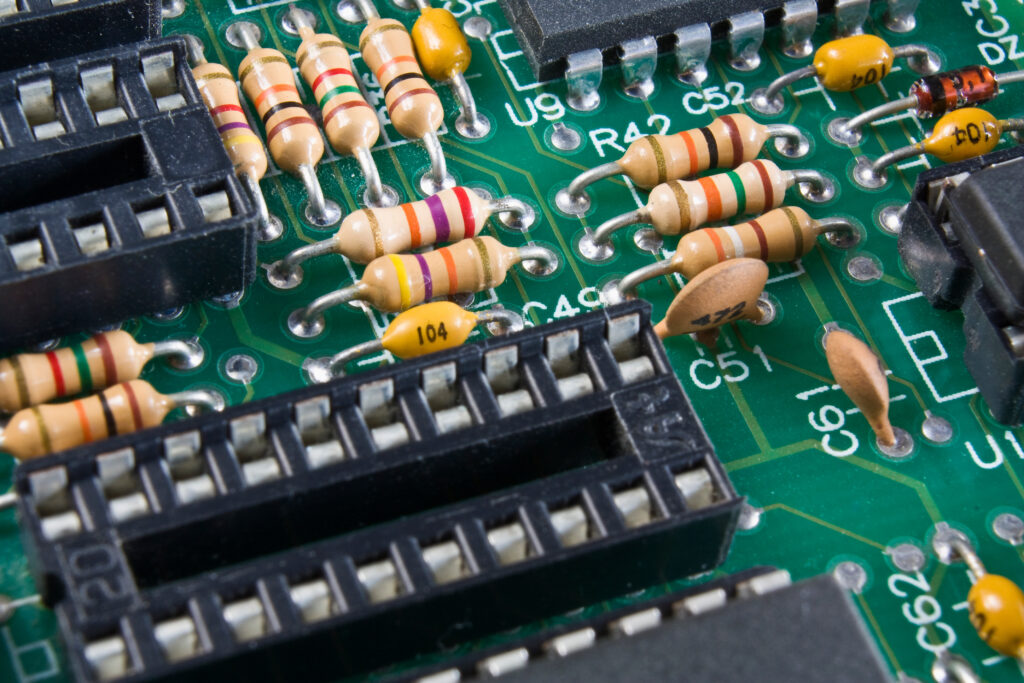
Wire Harnesses and Cable Assemblies
Wire harness manufacturers and cable assembly manufacturers offer a specialized service. It involves the assembly of wires, terminals, and connectors into a complete harness. This service is crucial for products that involve complex wiring systems.
Cable Assemblies vs Wire Harnesses
The difference between cable assemblies and wire harnesses is that cables often have a tougher cover or sheath. The coverings of a wire harness are meant to slightly shield and separate the wires, but a cable is made to resist the elements, like heat, water, and strain.
Based on desired use case and materials, wire harnesses can be designed to be extremely durable, even being used for automotive, agriculture, or other heavy-duty industries. Similarly, a cable assembly can be designed to be extremely light duty. Examples include items like USB cables.
Cable assemblies are often more costly due to their durability and expensive material.
Product Applications for Wire Harnesses and Cable Assemblies
Wire harnesses and cable assemblies find applications in various industries and products due to their ability to simplify complex wiring systems. Some common product applications include:
- Automotive Industry: Wire harnesses and cable assemblies are extensively used in vehicles for connecting various electrical components such as sensors, lights, and control systems.
- Aerospace and Defense: These industries rely on wire harnesses and cable assemblies for critical applications like aircraft wiring, missile systems, communication systems, and radar systems.
- Medical Devices: Wire harnesses play a crucial role in medical equipment, ensuring reliable connections between different components like sensors, monitors, and control units.
- Industrial Machinery: Wire harnesses are essential in industrial machinery for connecting motors, sensors, switches, and other electrical components to ensure smooth operation.
- Consumer Electronics: Cable assemblies are commonly found in consumer electronics like smartphones, laptops, and TVs, providing the necessary connections for power, data transfer, and audio/video signals.
Manufacturing Process of Wire Harnesses and Cable Assemblies
The manufacturing process of wire harnesses and cable assemblies involves several key steps to ensure quality and reliability:
- Reseach and product scope: Research of the application and requirements of the wire harness or cable assembly is conducted so that there is a clear understanding of the expectations of the wire harness or cable assembly that is being designed and manufactured.
- Design and Engineering: The process starts with designing the harness or assembly based on the specific requirements of the product and industry standards. This step also includes component selection.
- Wire Cutting and Stripping: Wires are cut to the required lengths and stripped of insulation at the ends to prepare them for termination.
- Crimping and Termination: Connectors and terminals are crimped onto the wires using specialized tools to create secure and reliable connections.
- Assembly and Routing: The wires, connectors, and other components are assembled according to the design specifications and routed through protective sleeves or conduits.
- Testing and Quality Control: Each harness or assembly undergoes rigorous testing to ensure proper connectivity, insulation integrity, and resistance to environmental factors.
- Final Inspection and Packaging: Finished wire harnesses and cable assemblies are inspected for quality and consistency before being packaged and shipped to the customer.
By following these steps and adhering to industry standards, manufacturers can produce high-quality wire harnesses and cable assemblies for a wide range of applications.
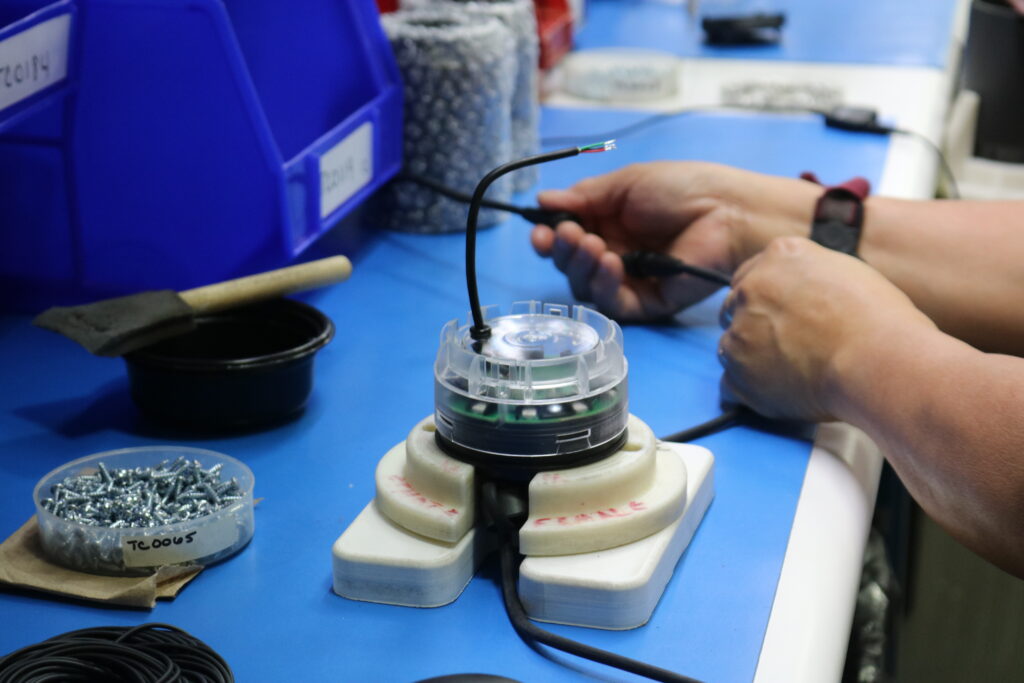
The Vetting Process: Factory Visits and Reference Checks
The vetting process is a critical step in selecting an electronics contract manufacturer. It involves verifying the manufacturer’s claims and assessing their capabilities firsthand. One way to do this is through factory visits.
A factory visit allows you to observe the manufacturer’s operations. You can assess their facilities, equipment, and processes. You can also gauge their organizational skills and attention to quality control.
Another important part of the vetting process is reference checks. Speaking with past or current clients can provide valuable insights. They can share their experiences and help you anticipate potential challenges.
Communication and Partnership: Building a Successful Relationship
Effective communication is key to a successful partnership with an electronics contract manufacturer. It ensures that both parties understand each other’s expectations and requirements. Regular updates and open dialogue can prevent misunderstandings and facilitate problem-solving.
Building a partnership goes beyond transactional interactions. It involves developing a relationship based on trust and mutual respect. This can lead to better collaboration and more successful outcomes. Remember, a good contract manufacturer is not just a service provider. They are strategic partners who can contribute to your business growth and success.
Hankscraft offers superior communication and expert support for our customers. Our team of engineers and project managers ensure your project’s success and manage the complex details. With a trusted contract manufacturer acting as an extension of your team, you’ll breeze through design for manufacturability, quality processes, regulatory compliance, product testing, and every other manufacturing step.
Financial Stability and Business Practices of Manufacturers
Assessing the financial stability of a potential electronics contract manufacturer is crucial. A financially stable manufacturer is more likely to deliver consistent quality and meet deadlines. It also indicates their ability to invest in new technologies and equipment.
Consider their business practices as well. Do they adhere to ethical standards? Are they committed to sustainability and environmental responsibility? These factors can impact your brand reputation.
In conclusion, a thorough evaluation of a manufacturer’s financial health and business practices can help you avoid potential risks and ensure a successful partnership.
Geographic Location and Its Impact on Your Choice
The geographic location of your electronics contract manufacturer can significantly impact your project. It affects logistics, communication, and overall project management.
For instance, a manufacturer located overseas might offer cost benefits. However, it could also present challenges such as language barriers, time zone differences, and complex shipping logistics.
On the other hand, choosing a local manufacturer can simplify communication and logistics. But it might come with higher costs. Therefore, it’s essential to weigh these factors when choosing a manufacturer.
Hankscraft’s business structure with a Wholly Owned Foreign Entity (WOFE) overseas in Suzhou, China, offers all the benefits of a local contract manufacturer with the added value of a global contract manufacturer. With Hankscraft handling the time-consuming details as your trusted contract manufacturing partner, communication and manufacturing project management become easy for you.
Flexibility, Scalability, and Custom Solutions
A good electronics contract manufacturer should offer flexibility. This means they can adapt to your changing needs, whether it’s a sudden increase in production volume or a shift in design specifications.
Scalability is another crucial factor. Your manufacturer should be able to grow with your business, handling increased demand without compromising on quality or delivery times.
Lastly, look for manufacturers that offer custom solutions. This could include design assistance, prototyping, or specialized manufacturing processes. Custom solutions can help optimize your product for manufacturability, potentially saving you time and money in the long run.
Intellectual Property Protection and Data Security
When outsourcing your manufacturing, protecting your intellectual property (IP) is vital. Ensure your electronics contract manufacturer has robust IP protection policies in place. This could include non-disclosure agreements or secure data handling protocols.
Data security is another critical consideration. Your manufacturer should have stringent data security measures to protect sensitive information. This is particularly important if your product involves proprietary technology or confidential customer data.
In conclusion, a reliable electronics contract manufacturer should prioritize IP protection and data security. These factors are crucial in maintaining your competitive edge and customer trust.
Preparing a Request for Proposal (RFP)
A Request for Proposal (RFP) is a crucial step in finding an electronics contract manufacturer. It outlines your project requirements, allowing potential manufacturers to provide detailed proposals.
Your RFP should include specifics about your project. This could be product specifications, volume requirements, and desired timelines. It should also ask for information about the manufacturer’s capabilities, certifications, and quality control processes.
In conclusion, a well-prepared RFP can streamline the selection process. It ensures potential manufacturers understand your needs and can demonstrate how they can meet them.
Conclusion: Making an Informed Decision
Choosing an electronics contract manufacturer is a significant decision. It requires careful consideration of many factors, from technical capabilities to business practices.
Ultimately, the goal is to find a reliable partner. One that can deliver high-quality products on time, while also aligning with your business values and objectives.
Learn More
Download your free PDF resource
Ensure you’re equipped with the essential questions for your upcoming meetings. Don’t miss out on this valuable resource to help you make informed decisions and find the perfect manufacturing partner for your project.
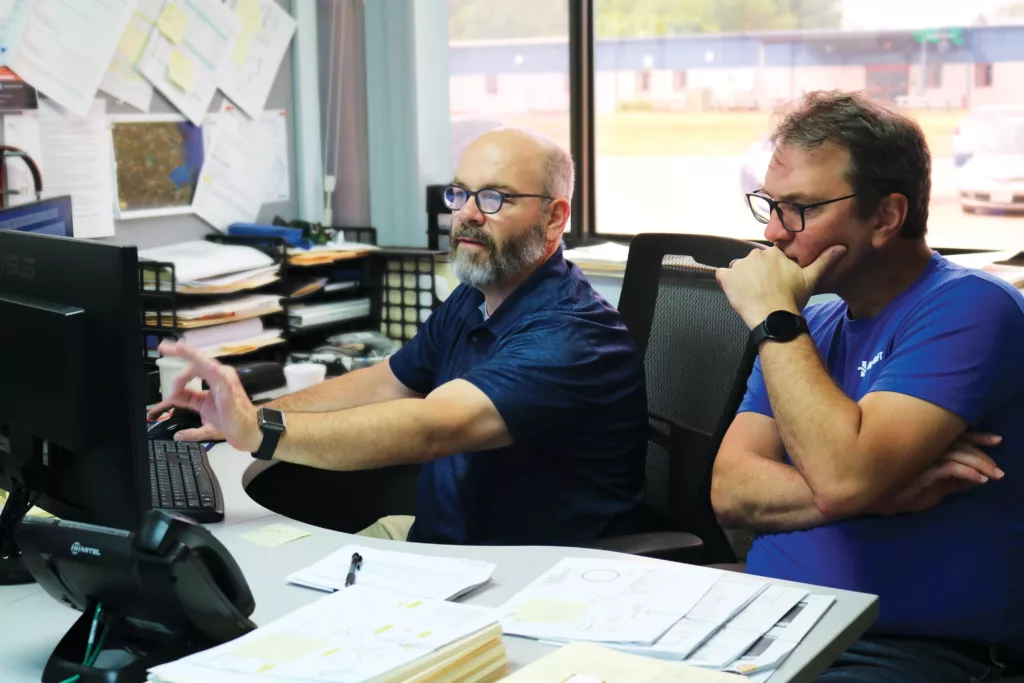