Contract Manufacturing
For more than 100 years, Hankscraft has been a trusted name in manufacturing, from our first patented product in 1920 to today’s complex assemblies. Our wealth of experience and expertise as an OEM provider will help you manage every unique product development and assembly challenge.
Dave Schoell
President – Hankscraft, Inc.
Industries we Serve
Hankscraft serves a wide variety of industries including HVAC, pet care, outdoor living, outdoor power equipment, home improvement, consumer appliances, and refrigeration. By providing high-quality, reliable, and innovative products tailored to each industry’s needs, we satisfy our customer’s unique requirements.
Electromechanical & Electronic Products
Industrial Projects
Pet Care
Residential Projects
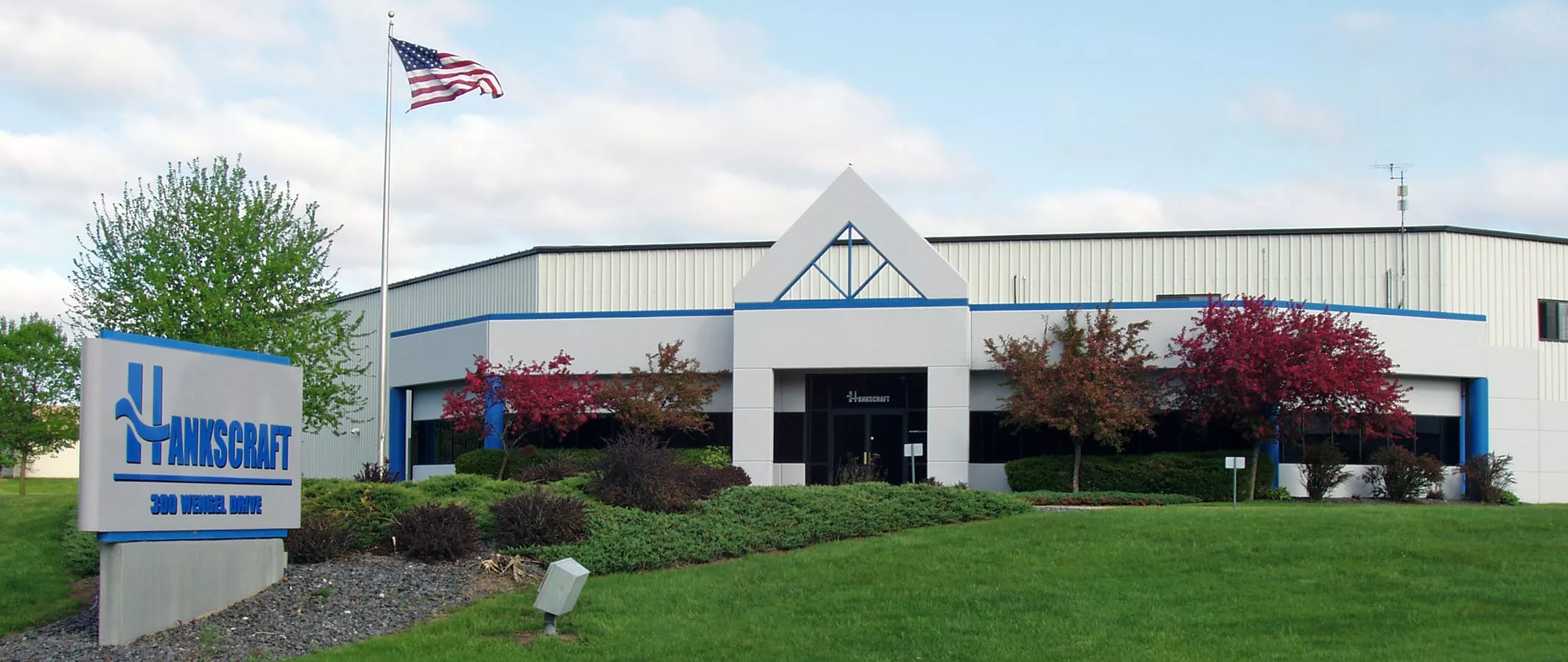
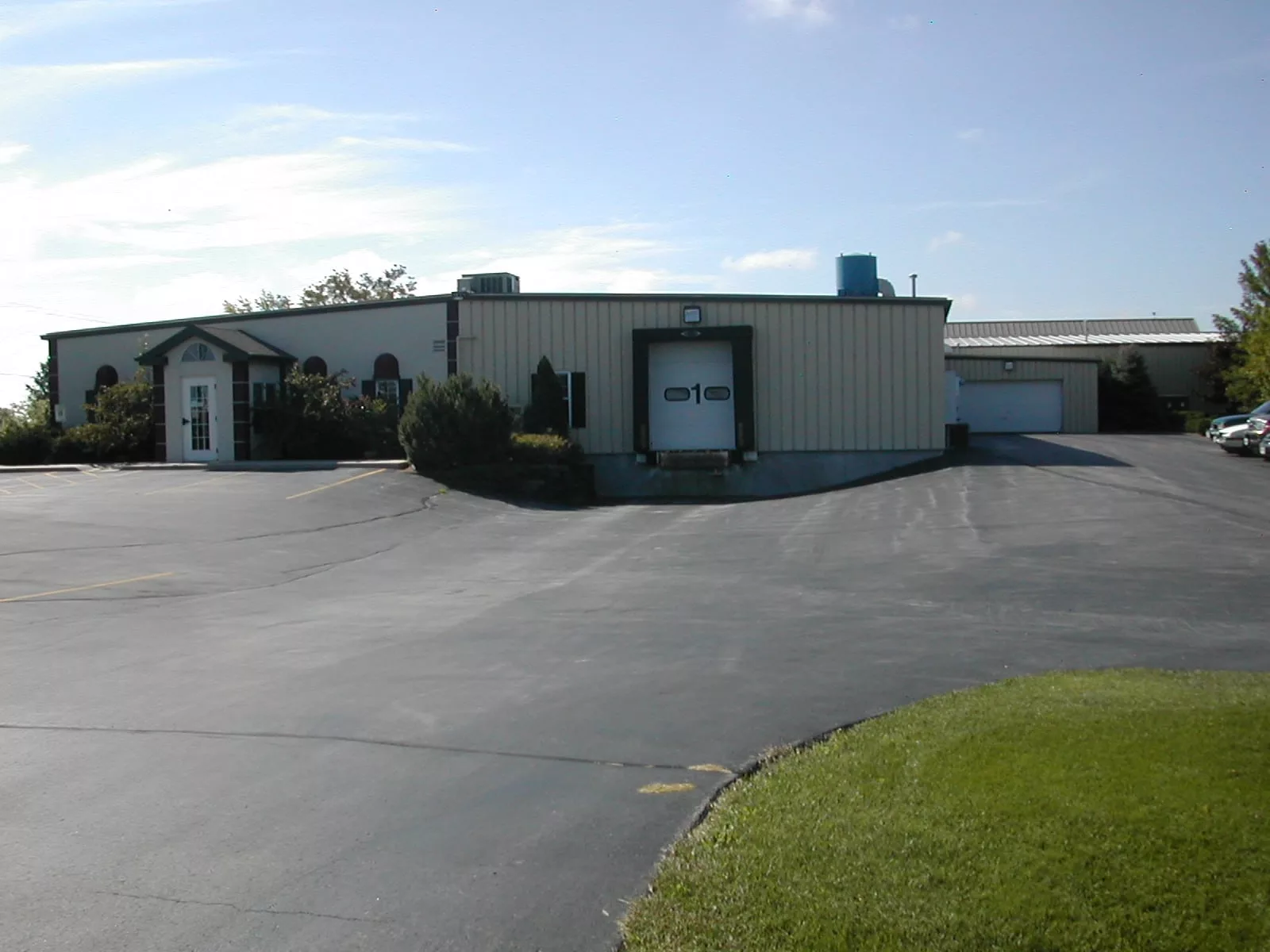
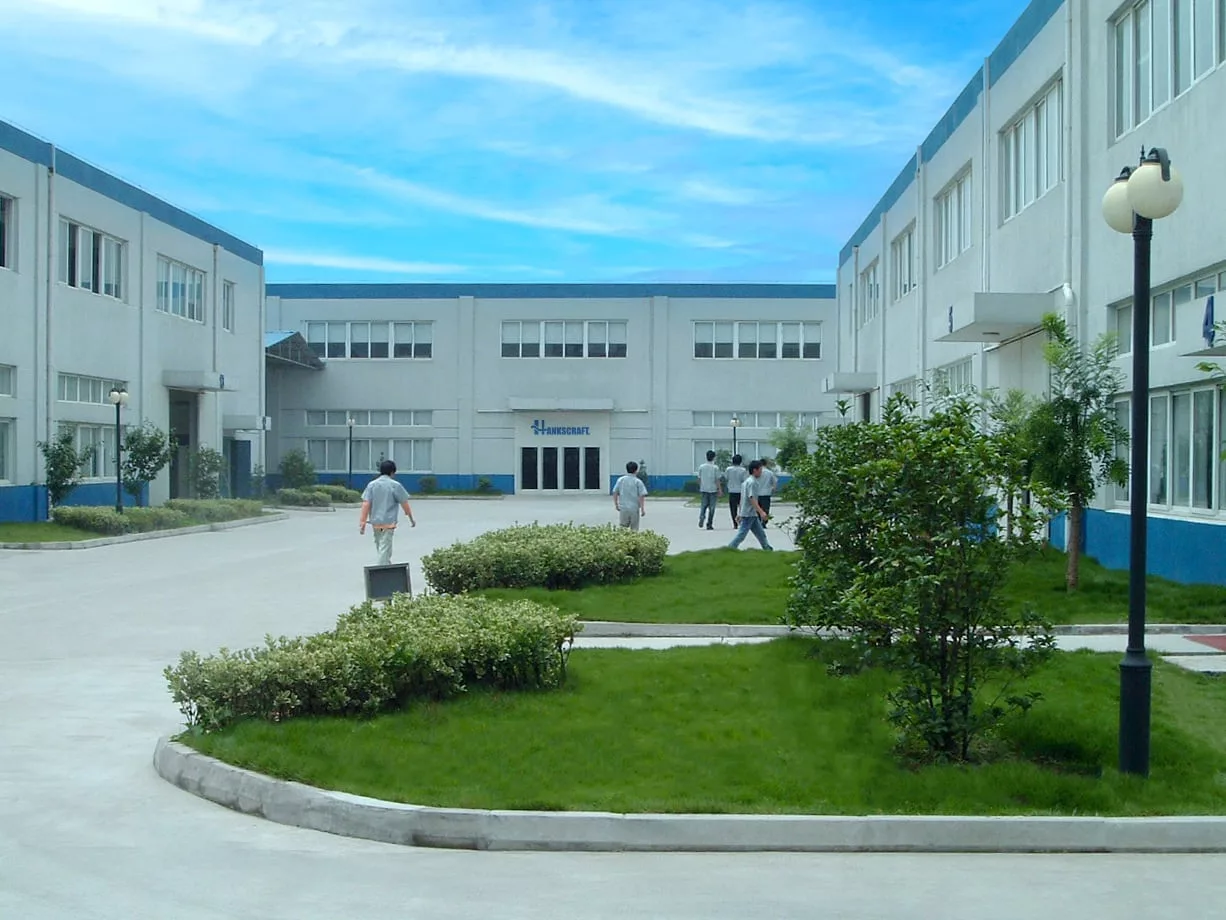
Hankscraft operates from four strategic locations worldwide: our headquarters in Reedsburg, Wisconsin; a manufacturing facility in Random Lake, Wisconsin; and two facilities in Suzhou, China. Our global presence allows us to offer rapid lead times while maintaining high quality standards.
Hankscraft operates from four strategic locations worldwide: our headquarters in Reedsburg, Wisconsin; a manufacturing facility in Random Lake, Wisconsin; and two facilities in Suzhou, China. Our global presence allows us to offer rapid lead times while maintaining high quality standards.
Hankscraft operates from four strategic locations worldwide: our headquarters in Reedsburg, Wisconsin; a manufacturing facility in Random Lake, Wisconsin; and two facilities in Suzhou, China. Our global presence allows us to offer rapid lead times while maintaining high quality standards.
Our Process
A partnership with Hankscraft is a collaboration, and the path to a successful product launch varies for each project. Our global resources and transparent project management ensure clear communication and give you confidence and control throughout the process.
Our involvement typically spans the following stages of development
Statement of Work (SOW)
We carefully review the project’s details, ensuring that every requirement is thoroughly reviewed. Our goal is to deliver a solution that meets your expectations.
Engineering Prints and 3D models
These documents and files serve as the project’s blueprint, capturing all product specifications. Our skilled team maintains effective communication and strong project execution.
Material specifications and qualifying
We thoroughly analyze materials for your project, ensuring that we meet your specifications and collaborating with you to review product validation and durability testing to meet your requirements.
Proof of concepts and prototyping
We bring your ideas to life through proof of concepts and prototypes. Design changes are accommodated, and prototypes are created to align with your preferences. Our approach ensures that your vision is realized.
Design Failure Mode Effect and Analysis (DFMEA)
Through DFMEA, we identify and address potential design failure modes. Our team evaluates components, functions, and interactions to mitigate risks and enhance the resilience of the final product. Informed decision-making and necessary modifications ensure a dependable outcome.
Process Failure Mode and Effects Analysis (PFMEA)
With PFMEA, we identify potential process failures and their impact on product quality. Our team assesses each step, implementing improvements and controls to ensure consistent product quality.
Bill of MateriaL (BOM)
A Bill of Material (BOM) is created that lists all the required components for your product. This ensures accuracy and efficiency in procurement and production, meeting the project timeline and budget.
Test Plan
We develop a comprehensive test plan to validate your product’s performance and functionality. Through various tests, we ensure it meets the required standards. By analyzing results and making necessary adjustments, we deliver reliable and high-performing products.
Design for Manufacturability (DFM)
We optimize the design for manufacturability (DFM), considering assembly ease, material selection, and cost-efficiency. Our team collaborates to enhance manufacturability without compromising functionality or quality. DFM streamlines production, improving quality, reducing cost, and ensuring efficient manufacturing processes.
Prototyping and production
We establish the correct steps for production release, utilizing established techniques including First Article Inspection (FAI), Pre-Production Approval Process (PPAP), Run at Rate (RAR), and engineering production builds. With attention to detail and strict quality control measures, we deliver a finished product that meets expectations.
Commitment to Quality
Hankscraft is committed to quality, following internationally recognized ISO practices while offering an ISO-certified production facility. Our dedicated Quality Engineering team continuously improves our processes for consistency, efficiency, and reliability. We deliver dependable, repeatable, and quantifiable KPIs that meet our customers’ requirements.
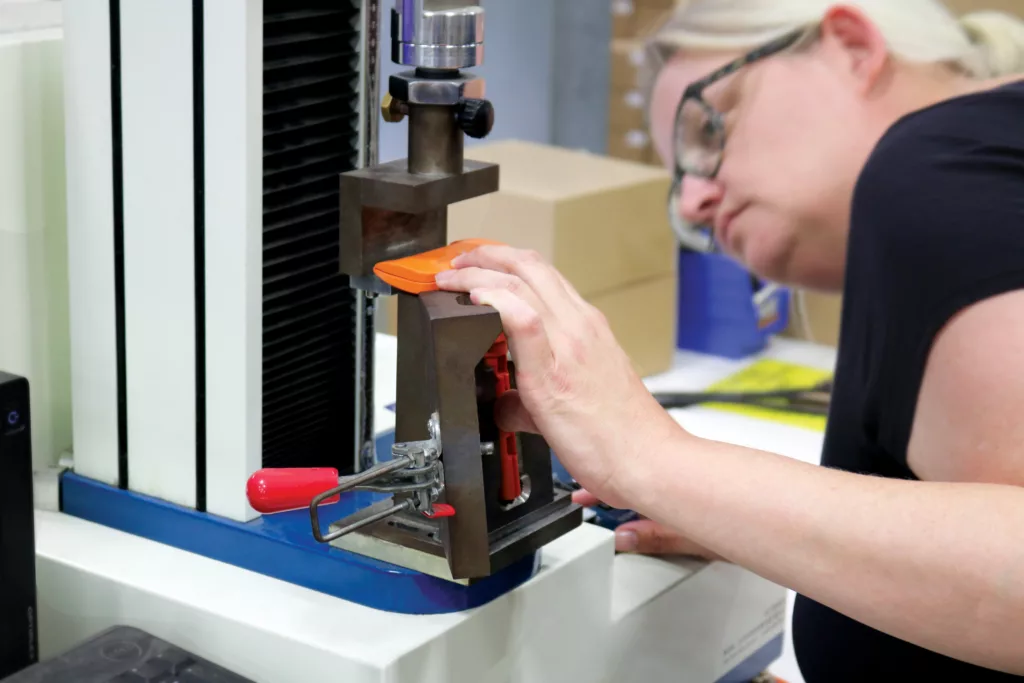
Start your project Now
Ready to get started? Hankscraft will be with you every step of the way as an invaluable partner, supplier, vendor, and extension of your team.
Contact us to learn more and to start your project.
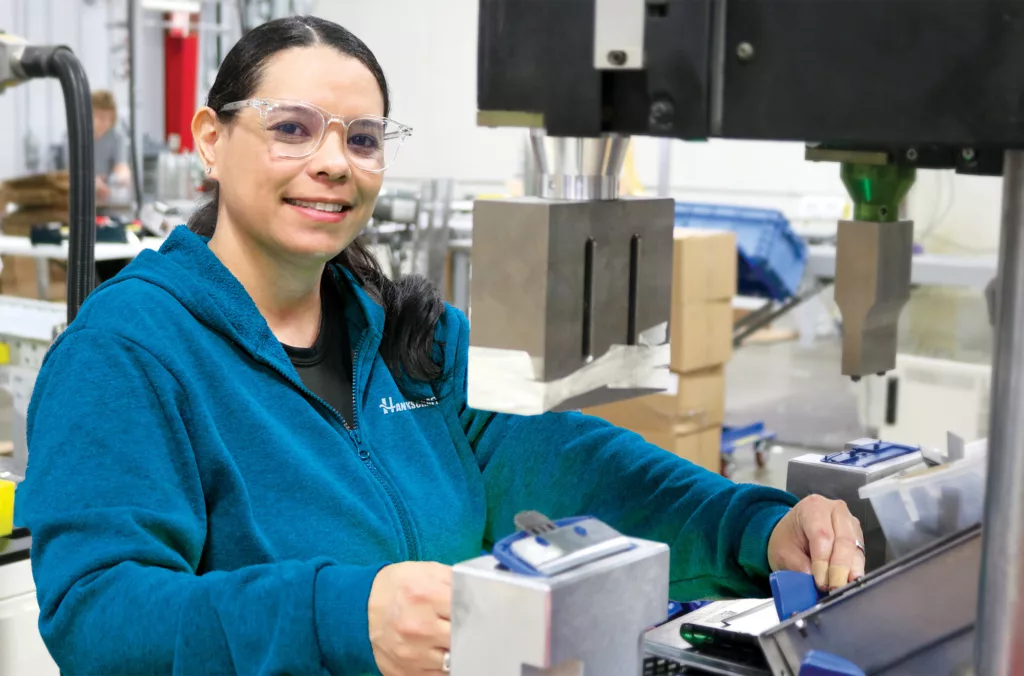